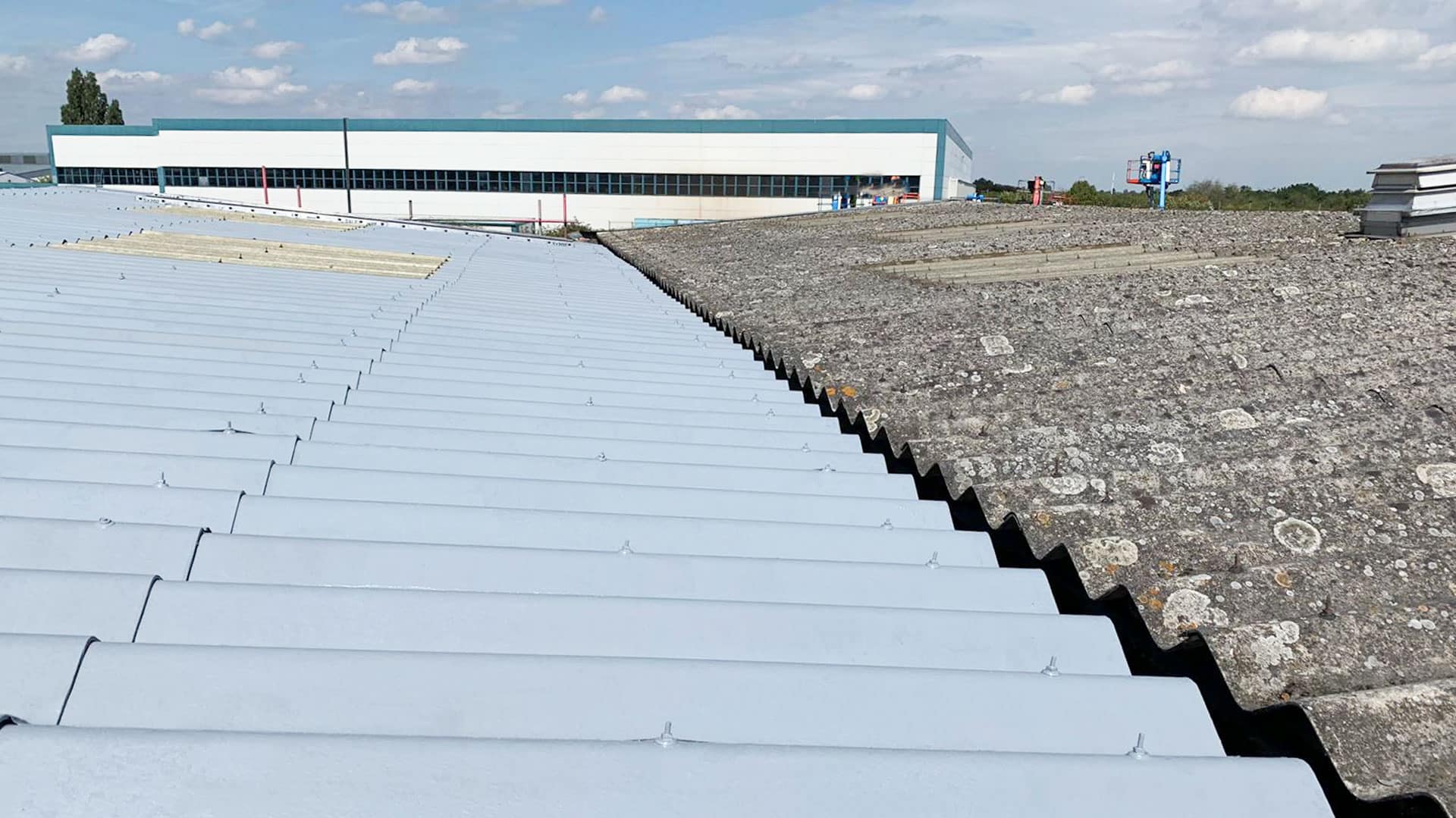
Asbestos is a general name for a family of six naturally occurring silicate fibres, chrysotile (white asbestos), amosite (brown asbestos), crocidolite (blue asbestos), anthophyllite, tremolite and actinolite. Asbestos fibres are strong, heat and chemical resistant and do not dissolve in water or evaporate.
Each fibre is composed of microscopic fibrils that can become airborne when damaged. Whilst brown and blue asbestos are by far the most dangerous, all forms of asbestos are now understood to cause serious respiratory health issues and prolonged exposure to this hazardous material can be deadly. All forms of asbestos have been illegal for use in new construction since November 1999.
The word asbestos derives from the Ancient Greek for “unquenchable” named from its use as wicks that did not burn. It is this very fire-resistant trait along with exceptional insulating properties, durability, strength and cost-effectiveness, that initially made asbestos such an appealing material for use in general construction and roofing before its serious health risks became apparent.
Asbestos has been used for thousands of years, but with the advent of the industrial era, the prevalence of its use increased from the mid 19th century. However, it was between 1950 and 1985 that the use of asbestos-containing materials (ACMs) reached monumental levels, being used in the construction of millions of homes, workplaces and public buildings.
Although blue and brown asbestos was banned in 1985 and all asbestos was subsequently made illegal in 1999, it is estimated that over six million tonnes of asbestos fibres were imported into the UK during the last century, peaking in 1973. Much of that asbestos is still present in our buildings today.
Considering this extensive usage, it is no surprise asbestos can be found mixed into the fabric of the building envelope. It is likely that at least half a million commercial properties and a million homes still contain some form of ACMs. Historically the roofing sector has used a variety of different ACMs including insulation, cement barge boards, roof tiles, corrugated asbestos cement, rainwater downpipes, cladding and fascias.
With the introduction of the Control of Asbestos Regulations 2012, the ‘duty to manage’ asbestos became a legal obligation for:
If you own, lease or are responsible for the maintenance of a building, the Control of Asbestos Regulations 2012 requires you to manage the risk from asbestos by:
Whilst this is certainly daunting, Garland UK can provide a single point of contact to guide you through these challenges. Our highly skilled Technical Managers have completed extensive asbestos training, to ensure that no one is put at risk.
Garland UK can arrange a thorough asbestos survey to evaluate your roof condition as part of a project’s pre-assessment, ensuring it is dealt with suitably, in accordance with the latest Control of Asbestos Regulations 2012 (CAR 2012).
If you suspect that your roof may contain asbestos materials, here are a few things to consider, to ensure your asbestos roof handling can be resolved safely whilst following the industry best practices.
Since 2009, land remediation relief has been available to any registered UK company that undertakes work to investigate and remove or contain any contamination hazardous to human health, present when the building was purchased. This allows for a 150% tax relief off of your taxable profits. It does however take time for that process to happen and has a large initial expenditure which is why covering or encapsulating is sometimes preferred.
In some instances, it is not necessary to completely remove and dispose of asbestos roofing and instead a method of encapsulating or covering is preferred. The disposal costs for removing asbestos can be substantial and can cause significant delays on your build project, so it is something to consider when exploring your disposal options with a roofing expert.
In every instance, measures must be made to avoid the risk of exposure to asbestos or disturbing the asbestos fibres. When assessing the best course of action for your roof, it is important to consider what processes will need to be put in place to avoid any risk of asbestos exposure on your project, as this can cause necessary but significant delays to the project delivery and additional budget constraints. Expert advice is essential in managing this risk.
Garland UK has a national network of approved contractors with extensive expertise and training who you can trust to complete your work safely and to the highest professional standard all supported by our up to 25 year Garland UK Single-Point Guarantee.
Prior to removal of asbestos, an Asbestos Survey must be carried out in line with HSG 264 (2012). It is the responsibility of the contractor to ensure that any work carried out on asbestos-based or asbestos-cement components complies with the Asbestos (Licensing) Regulations, the Control of Asbestos at Work Regulations and all requirements of the Health and Safety Executive, including Codes of Practice and guidance A0, A9 and A12.
Detailed Health and Safety Procedures, together with method statements, must be submitted as part of the Health and Safety Plan with regard to any works to clean, remove or dispose of Asbestos based products.
Asbestos cement sheet roofs are fragile; therefore, no work should be started until the client is satisfied that a competent contractor with sufficient experience is appointed and that adequate procedures (RAMS) are in place before commencing works.
There are a number of different solutions to dealing with your asbestos roof. Put simply it boils down to either removal, over-cladding or encapsulation. Every project is unique and our Technical Managers are always on hand to help you decide which solution is right for your requirements.
The complete removal, disposal and replacement of your asbestos roof is certainly the most aggressive solution to the problem. With a completely new roof structure installed, you can take advantage of all the latest roofing materials and technologies to improve your roofs thermal performance, lifespan and visual aesthetic.
It is however also comparatively time-consuming and labour-intensive, causing longer construction times and increased disruption to the site. This and the increased amount of asbestos disposal inevitably make this a costlier proposition.
Over-cladding asbestos over-cladding is a fast, safe and far cheaper alternative to costly asbestos removal. Utilising products such as Garland UK’s R-MER CLAD metal roof system, it is now possible to overclad the roof structure whilst leaving the existing asbestos roof in place. Whilst some cleaning may be desirable, over-cladding minimises the need to interfere with the asbestos roof structure.
This is predominantly limited to securing the mechanical fixings, using the latest HSE guidance to suppress dust creation, onto which the new system is installed. This safely encapsulates the asbestos and prevents future damage and deterioration whilst also providing a major aesthetic improvement and allowing for increased insulation, significantly improving the roof’s thermal performance to standard.
Coating or encapsulation utilises cold-applied liquid systems, such as Garland UK’s Dura-Coat or White Knight, to fully cover and encapsulate the existing asbestos sheets eliminating the risks of airborne asbestos. These innovative solutions provide a fast, safe and far cheaper alternative to costly asbestos removal. There are different benefits to each system, so it is always best to talk to your local Garland Technical Manager to find out what will work best for you.
The existing roof is carefully prepared, repairing minor issues and replacing badly cracked and damaged roof sheets with sheets of a similar profile. Fixing bolts that are damaged are replaced. The roof is then cleaned by asbestos specialists using a dedicated process to clean and prepare asbestos roofing sheets in a safe, streamlined and thorough manner. Finally, the cold-applied liquid system is applied and allowed to cure.
“Asbestos can be a challenging material to deal with, but thanks to a range of innovative waterproofing system technologies, we are well equipped to encapsulate and cover asbestos safely, reducing our customer’s costs and providing the technical advice they need to mitigate risk every step of the way.”
Sam Rigden, Technical Manager, Garland UK