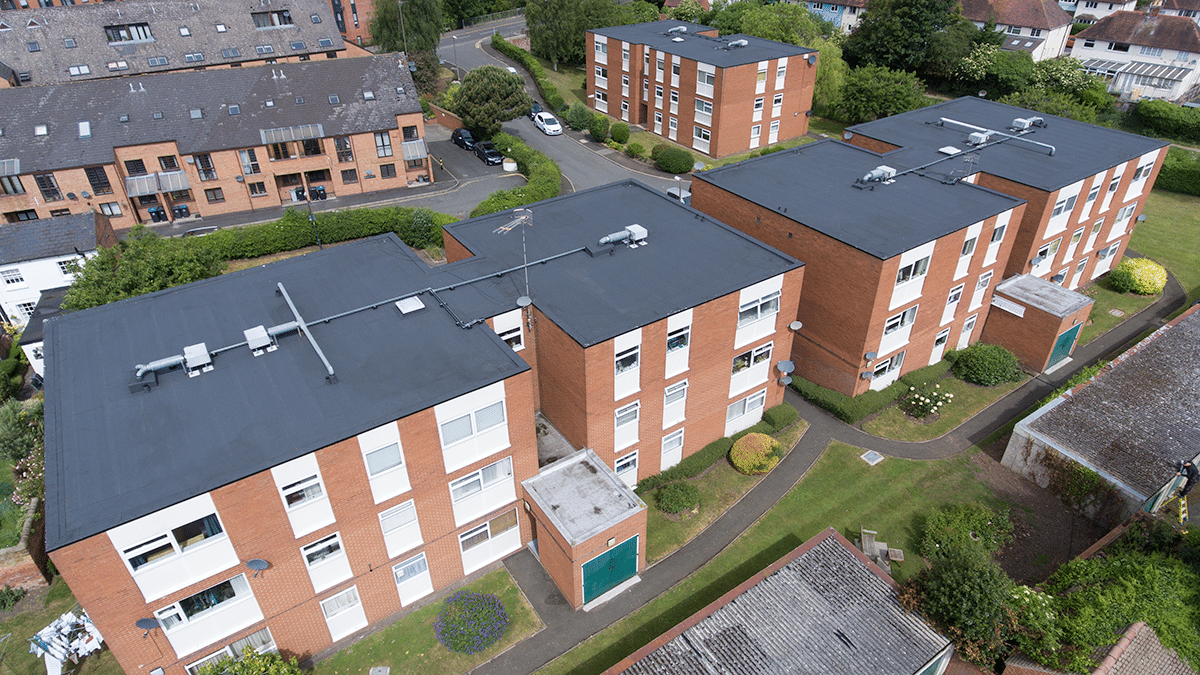
By their very nature, all construction projects involve significant risk. Whilst the construction industry is steadily improving, its rates of ill health, severe injury and deaths are still the highest of all UK industries. Sadly, almost 1 in 5 deaths in construction occur during work on roofs. It is essential in every project that risks are carefully assessed and, where they cannot be designed out, a mitigation strategy is properly planned and implemented.
In this article, we’ll look at the risks involved with roof refurbishment, the relevant regulations that apply and how Garland UK can help you mitigate or eliminate those risks from your project.
The first risk that should be considered is the structural stability of the existing building itself. Unlike a new build project, where the structure has been specifically designed to accommodate the chosen roofing option, a detailed structural survey is essential in a refurbishment.
This allows the existing building to be fully understood and can accommodate the structural load of the new roof. Importantly for all roofing work, it is necessary to assess the fragility of the existing roofing surface and roof deck. We recently highlighted the historical use of structurally unsound RAAC roof decks, which created exactly the type of structural risk that should be taken into account.
For a roof refurbishment to take place, it is necessary for both assessment and construction work to take place at heights and a worthy consideration for mitigating risk. This creates the risk of falls occurring, a serious risk to people working on the roof and to people below from falling tools and materials.
Areas that are at high risk include:
Fire Risks in Construction
The risk of fire during roof refurbishment is predominately due to the need to perform what is known as hot works, which BS 9999:2017 defines as “any procedure that might involve or have the potential to generate sufficient heat, sparks or flame to cause a fire”.
The hot works associated with roof construction are:
Last year hot works accounted for approximately one-fifth of construction-related fires. The majority of these were caused by the use of gas torches whilst drying the roof substrate.
Risks associated with roof fires include:
As with all types of construction, roof refurbishment work can involve the risk of exposure to a variety of potentially harmful dust, materials and chemicals. To mitigate risk, exposure should be considered in both the removal of the existing roof and the installation of the new roof. Of particular concern when undertaking roof refurbishment work are the following:
There are a number of regulations and guidance documents that specify your statutory obligations if you own, lease or are responsible for the maintenance of a building, as well as the duties of the designers and contractors involved with the roof refurbishment work itself. By complying with these rules, you can ensure that the risks previously outlined can be avoided, prevented and mitigated. Whilst this can seem daunting, Garland UK’s highly skilled Technical Managers are on hand to help you navigate these challenges.
The Work at Height Regulations 2005 (WaHR), produced by the HSE, apply to all work at height where there is a risk of a fall liable to cause personal injury. The regulations include duties for employers, the self-employed and any person who controls the work of others, including facilities managers and building owners who may contract others to work at height. They should ensure that:
WaHR set out a simple hierarchy for managing work at height and selecting appropriate equipment:
Where this is not possible or practical, personal fall protection equipment such as anchor points and anchor line systems can be used. However, a higher level of training will be necessary, and the number of workers protected by these systems will be limited.
Building Regulations Approved Document K (2013) provides advice on protection from falling, involves fitting safety measures on staircases, ramps and ladders, and advice about the positioning of balusters, vehicle barriers, and windows to avoid injury.
If there is permanent access for people onto your roof then guarding must be installed to provide protection from falling at edges, roof lights and any other openings.
CDM (2015) is overarching health and safety legislation that defines the roles and legal responsibilities of everyone involved with any part of a building project.
As designated CDM (2015) designers, our Technical Managers are on hand to offer their expert recommendations. After completing a complimentary detailed consultation and site visit, we can help:
We will provide a bespoke specification for your particular roofing needs, with the best system for your building type and budgetary requirements. This specification will always have assessed and designed out or significantly reduced risks.
For example, to mitigate the risk of fire, we will always specify flame-free systems wherever possible and provide clear, flame-free installation instructions to our approved contractors to ensure that all work follows NFRC Safe2Torch guidelines at all times. Please read our “When to include flame-free systems in your roofing project” for a more detailed look at the advantages of our flame-free systems.
In July 2017, the National Federation of Roofing Contractors (NFRC) introduced the Safe2Torch scheme, with the aim of reducing the risk of roof fires in the flat roofing industry caused by the use of gas torches. This is achieved through the application of the following principles.
Safety through design
Those who create risks have a responsibility to manage those risks. Therefore, it is essential to make sure all fire risks are identified at the survey stage, so their mitigation can be designed in from the inception of the project.
High-risk areas must be identified and suitable flame-free systems specified for use in these areas. Importantly, where it is impossible to determine the make-up of the roof, Safe2Torch treats these areas as high-risk by default. Torch-on applications are only permitted in areas that are demonstrable to be safe.
Installing contractors have as much a responsibility as designers in making the construction process as safe as possible. Contractors must perform their own risk assessments, not only before the project starts but also continually as work proceeds, as risks that were unknown during the design stage may reveal themselves during the construction process.
Flame-free exclusion zones are created, within which only flame-free roofing products may be used, extending 900mm from any or unknown combustible material or high-risk details. Again, if there is any doubt at all, a flame-free solution must be used by default. Only if it is demonstrable that an area is safe can torch-on applications be used.
Eliminating or Mitigating Roof Refurbishment Risks
Garland UK understands the risks involved with your roof refurbishment. Our Technical Managers have a wealth of training and expertise, allowing them to identify risks and, importantly, make sure that risk is designed out or mitigated in every specification. Garland UK only provides roofing solutions in which we have complete confidence, with a mission to raise standards in the industry and do the right thing for our clients.
Garland UK has a national network of approved contractors with extensive expertise and training in managing risk on-site, who you can trust to complete your work safely and to the highest professional standard, all supported by our leading Single-Point Guarantee.
“These steps can be taken to help ensure that the risks associated with your roofing refurbishment project can be avoided, prevented and mitigated.”
Jack Costello, Technical Manager, Garland UK