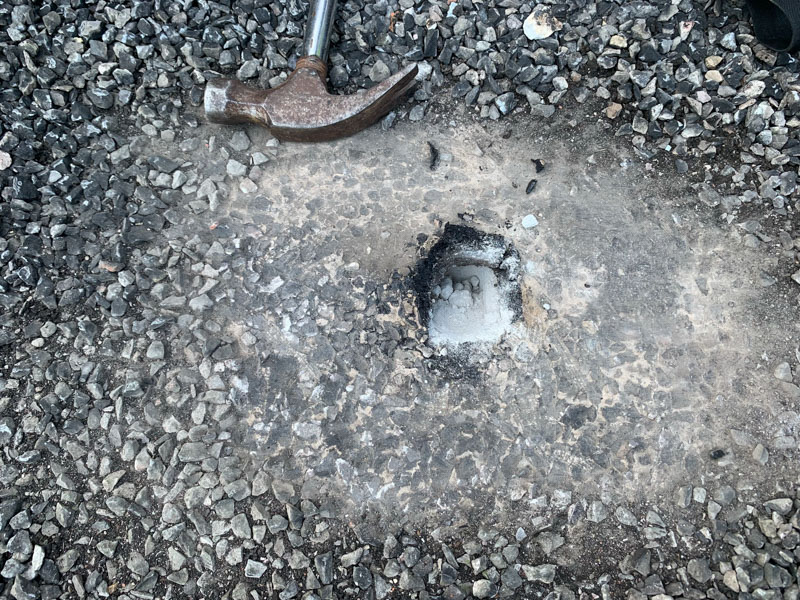
Reinforced Autoclaved Aerated Concrete (RAAC) is a form of steel-reinforced lightweight concrete. Autoclaved Aerated Concrete (AAC) was first created in Sweden in the 1920s as a significantly lighter alternative to traditional concrete mixes and was utilised to create lightweight masonry blocks of the type still commonly used today. By the early 1930s, steel reinforcement had been incorporated to create RAAC, allowing for significantly larger structural units such as wall panels, and floor and roof planks.
RAAC products are formed by mixing cement, lime, extremely fine sand or pulverised fuel ash and calcined gypsum. Aluminium powder and water are then added to form a concrete slurry, which is cast in a mould containing the steel reinforcement. The aluminium powder chemically reacts with the lime and water to produce small bubbles of hydrogen gas, which causes the mixture to foam, more than doubling its volume. The hydrogen evaporates into the atmosphere when this foaming reaction finishes, leaving a lightweight cellular concrete mixture. Finally, the mould is removed, and the product is cured at both high temperature and pressure in an autoclave for around 12 hours, which causes the sand and lime to fuse into a form of calcium silicate hydrate crystal, increasing the strength of the finished product.
RAAC products were first introduced into the UK market in the 1950s and, until the mid-1980s, were increasingly used in the construction industry. Due to its lightweight, fire resistance and thermal performance, RAAC became popular in roof decks and was extensively used in both commercial buildings and, particularly, in public sector buildings such as schools, colleges and hospitals.
Unfortunately, RAAC’s lightweight properties came at the cost of its structural strength. RAAC does not perform in the same way as traditional reinforced concrete, being significantly more prone to deflection. Due to its porous nature, reinforced steel is more vulnerable to corrosion, so a protective coating of latex cement or bitumen is needed. The ACC also bonds poorly with the reinforcement steel, requiring welded crossbars to secure it in place.
By the 1980s, RAAC roof planks installed in the 1960s had begun to fail. Subsequent case studies revealed significant underlying issues with the RAAC roof planks. The steel reinforcement was often insufficiently covered, allowing corrosion to occur. Many roof planks had a high span-to-depth ratio, meaning they did not have suitable capacity to span between bearing points. Often, the steel reinforcement did not extend throughout the complete length of the product and contained an inadequate number of welded crossbars.
In 1996, the BRE published an Information Paper stating that excessive deflections and cracking had been identified in many RAAC roof planks, and there was evidence that reinforcement corrosion had occurred. In 2002, the BRE released further information on the performance issues of RAAC roof planks, advising that, although in-service performance was judged to be satisfactory, it would be prudent to monitor their actual performance after a number of years. It was determined that the lifespan of RAAC roof planks was about 30 years. As this construction was last used in the 1980s, all RAAC roof decks have now exceeded their estimated lifespan and may require to be replaced in their entirety.
In late 2018, the Local Government Association (LGA) and the Department for Education (DfE) alerted all school building owners about the partial collapse of a flat roof at an Essex school constructed from RAAC roof planks, which occurred with little warning. Fortunately, this happened at a weekend when the building was unoccupied. The school had recently had a new roofing membrane installed, which may have increased the load across the roof. It was also suspected that its darker colouration may have increased the amount of thermal heating to which the RAAC roof planks were exposed, contributing to the failure. All schools and education estates were advised to immediately assess their assets to identify any RAAC roofs, perform a risk assessment and take remedial action where necessary.
The Standing Committee on Structural Safety (SCOSS) released an Alert in May 2019 highlighting that this is a broader issue, as RAAC roof planks were used across many types of buildings. They highlight a case of damage that occurred to RAAC roof planks at a retail premise in early 2019.
Following this Alert, NHS England identified several hospitals with RAAC roof planks and serious structural concerns. West Suffolk Hospital, for example, has now had to install 27 metal supports under the RAAC roof planks to mitigate the immediate risks. The Government then set aside £100 million to continue to carry out this urgent remediation work at hospitals affected by RAAC roof plank issues.
As there is no central register of buildings that use RAAC roof planks, a physical inspection conducted by a qualified structural engineer or building surveyor is the best way to identify if your roof deck is constructed using RAAC.
Due to the potential dangers involved, a detailed risk assessment must be carried out, and a safe system of work must be planned to allow this identification and inspection to occur.
An owner or building manager can take some steps to assess the probability that they may have a RAAC roof deck:
If you suspect that you do indeed have a RAAC roof deck, then the Standing Committee on Structural Safety (SCOSS) offers some warning signs that you should look out for that may indicate that your roof is at serious risk of failure:
Garland UK’s highly skilled Technical Managers are on hand to help. Once RAAC has been identified, a local Technical Manager will conduct a site visit of your building, providing a detailed assessment of the thermal and weathering condition of your roof and an efficient RAAC remediation plan that details the removal of the RAAC panels and roof replacement, in line with structural engineer guidance.
A structural engineer or suitable building surveyor must be commissioned to report on the condition of the deck, and if found to be in good structural condition, they may deem it possible to overlay it with a new membrane.
However, at Garland UK, it is our strong advice that considering the life span of RAAC roof planks has now been exceeded, this is unlikely to be feasible or safe. Garland UK would not recommend retaining or working on existing RAAC decks.
If a RAAC roof is discovered, we will always recommend to our clients that the RAAC roof should be completely removed and replaced with a new structurally sound deck, keeping your building safe and protected for years to come.
Garland UK has a national network of approved contractors with extensive expertise and training who you can trust to complete the RAAC remediation work safely and to the highest professional standard, all supported by our high-performance waterproofing systems industry-leading Single-Point Guarantee.
“RAAC roof planks were last installed in the 1980s and have now exceeded their 30-year life span. If discovered, we would always recommend their complete removal and replacement with a new roof deck to ensure the continued safety of your building.”
Ben Whitemore, Technical Product Manager, Garland UK
Reinforced Autoclaved Aerated Concrete (RAAC) is proven to be weaker than traditional concrete. RAAC is commonly found in the roof structures of UK buildings built between the 1950s-1980s.
Reinforced Autoclaved Aerated Concrete (RAAC) is a form of steel-reinforced lightweight concrete created in the 1920s as a lighter pre-formed alternative to traditional concrete mixes.
RAAC products were first introduced into the UK market in the 1950s and, until the mid-1980s, were increasingly used in the construction industry. Due to its lightweight, fire resistance and thermal performance, RAAC became popular for use in roof decks and was extensively used as such in both commercial buildings and, particularly, in public sector buildings such as schools, colleges and hospitals.
RAAC’s lightweight properties came at the cost of its structural strength. RAAC does not perform the same way as traditional reinforced concrete and is significantly more prone to deflection. By the 1980s, RAAC roof planks installed in the 1960s had begun to fail.
Case studies have revealed significant underlying issues with RAAC roof planks. The steel reinforcement was often insufficiently covered, allowing corrosion to occur. Many roof planks had a high span-to-depth ratio, meaning they did not have the suitable capacity to span between bearing points. Often, the steel reinforcement did not extend throughout the complete length of the product and contained an inadequate number of welded crossbars.
The typical lifespan of RAAC roof planks is roughly 30 years. As this construction was last used in the 1980s, all RAAC roof decks have now exceeded their estimated lifespan and are required to be replaced in their entirety.
In late 2018, the Local Government Association (LGA) and the Department for Education (DfE) alerted all school building owners about the partial collapse of a flat roof at an Essex school constructed from RAAC roof planks, which occurred with little warning. Fortunately, this occurred at the weekend when the building was unoccupied. All schools and education estates were advised to immediately assess their assets to identify any RAAC roofs, perform a risk assessment and take remedial action where necessary.
As there is no central register of buildings that use RAAC roof planks, a physical inspection by a qualified structural engineer or building surveyor is the best way to identify if your roof deck is constructed using RAAC. An owner or building manager can take some steps to assess the probability that they may have a RAAC roof deck
If you suspect that you have a RAAC roof deck, there are some warning signs that you should look out for that may indicate that your roof is at serious risk of failure. If the roof has recently leaked or is leaking, or ponding can be seen on the roof, there is cause for concern. This can potentially point to the RAAC planks deflecting.
If a RAAC structure is identified, we will always recommend to our clients that the RAAC roof deck should be completely removed and replaced with a suitable timber or metal deck, keeping your building safe and protected for years to come.