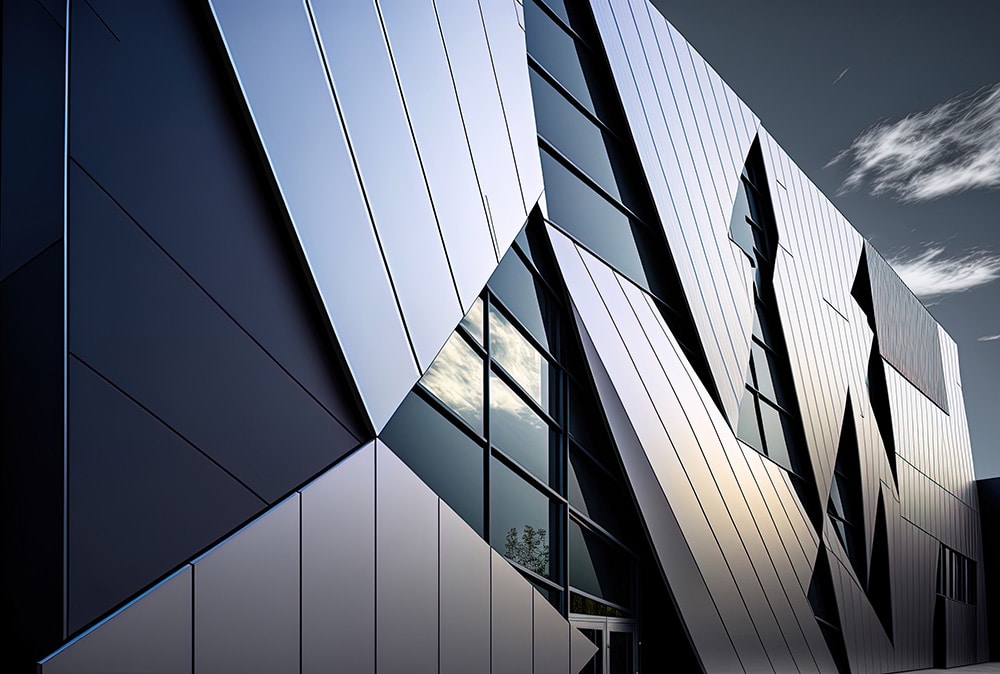
Facade or exterior cladding systems are critical components of modern construction that combine functional and aesthetic elements as an external envelope and are essential in forming a building’s visual identity. They are comparatively easy to install in both newbuild and retrofit applications. Importantly, they can accommodate increased thicknesses of thermal insulation, helping to improve a building’s sustainability whilst protecting it from the elements. For these reasons, facade systems are becoming increasingly popular with specifiers.
The design of facade systems has evolved significantly over time to allow for cladding in almost any material; ceramics, glass, plastics, stone, wood and even living green facades are all commonly used, but for both longevity and performance, you cannot choose better than metal facade systems.
In its simplest form, metal facade systems are formed with two main layers: A substructure frame fixed directly to an SFS system or back to a masonry structure. The next layer is a metal facade panel attached to the substructure to provide the space needed to incorporate thermal insulation. Metal facade systems are non-structural, supporting their own weight and any additional wind loads.
A ventilated facade is a design that incorporates an air gap between the insulation and the backside of the facade panel. This gap, strategically open at both the top and bottom, allows natural ventilation to circulate throughout the facade. Ventilated facades serve a dual purpose of safeguarding the structure against weather elements with an outer skin while fostering a healthy indoor environment through ventilation and insulation. This innovative architectural technique is commonly referred to as rainscreen cladding.
Most metal facade systems consist of several interlocking panels forming an external waterproofing layer. These interlocking panels usually snap into place to form a weatherproof barrier. But importantly, the ventilation gap still allows the building to breathe, releasing any water vapour from the substructure. Ventilated facade systems improve overall thermal and acoustic performance and, combined with the breathable design, equalise internal and external pressures.
Metal facade systems are available in aluminium, aluminium zinc alloy, copper, steel and titanium zinc alloy. Depending on the chosen material, they can also be colour-coated or left as a natural finish. This provides the flexibility to balance your project’s aesthetic and budgetary requirements.
They are also known for their exceptional durability. Whilst steel panels are galvanised colour-coated to maintain longevity, aluminium, copper, and zinc possess a degree of self-healing ability, forming a protective patina when exposed to the atmosphere, making them the longest life-span facade systems available.
This long lifecycle helps to make metal facade systems very cost-effective. Notably, combined with their lightweight, it also helps to make them highly sustainable by minimising Embodied Carbon emissions. Furthermore, when they finally reach the end of their life, metal systems are straightforward to recycle, forming a circular economy.
The incorporated thermal insulation helps to make buildings more energy efficient, saving money for the building occupiers and lowering the Operational Carbon of the building as a whole. Therefore, metal facade systems are one of the most sustainable options for your building envelope, maintaining the highest level of sustainable building practice.
When considering the life cycle of the products used on a project, the reduced embodied carbon is an intrinsic part of a BREEAM evaluation.
Life Cycle Costing is utilised to assess the sustainability of a project providing up to 4 credits. It is also crucial to achieving the highest Building Design and Construction (BD+C) and Building Operations and Maintenance (O+M) LEED certification.
One of the main reasons for facade systems’ increasing popularity is just how adaptable these systems are to any design needs. Various colours, coatings and finishes are on offer, and manufacturers can produce panels in varying panel forms and widths. They can be installed diagonally, horizontally or vertically, enabling almost unlimited architectural design freedom so the ideas you put on paper can become a reality.
Of course, to allow for this design freedom, it is essential to carry out a thorough structural analysis if specifying an existing building. Metal facade systems are a relatively lightweight construction, minimising the structural load on the building. Still, with more complex designs, this can increase, as can the wind load across the surfaces.
With metals, in general, the incompatibility of materials must always be considered. Different metals tend to react poorly with each other. For example, when placed together, copper and zinc cause bimetallic corrosion, also known as Galvanic corrosion, the chemical reaction used to power batteries!
The addition of thermal insulation is usually desired, but its performance can be maximised by selecting a system that reduces any thermal bridging between the facade and the rest of the building, leading to a reduced wall to panel distance.
Modern metal facade systems usually snap into place, tightly interlocking the panels, making installation simple and very quick. As stated earlier, this does not affect the quality of the waterproofing, but it does allow the facade to breathe. This ensures that the metal facade and any thermal insulation are kept at peak performance by removing any water vapour that may condense.
When designing a facade system, special care must be taken to prevent potential leakage points and optimise the thermal performance of a building, where using the correct attachment to your building’s structural elements is paramount. Properly installed to the manufacturer’s specifications, a ventilated metal facade will allow for thermal expansion and contraction within the system and ensure thermal bridging is reduced.
Choosing the right installer trained in the proper installation techniques for your facade system is always essential. Garland UK has a national network of approved contractors with extensive expertise and training who you can trust to complete your work safely and to the highest professional standard, all supported by our up to 30 year Garland UK Single-Point Guarantee.
As with roofing, annual inspections are needed to identify any maintenance required quickly. Problems spotted early can be fixed quickly and cost-effectively. This ensures that you maximise the longevity of the metal facade. With all metal facades, you should watch out for any damage to panels, flashings and mastic seals.
Garland UK believes in partnering with you for the life of your building. As part of our PartnerCare service, the Garland UK aftercare programme will provide regular inspection reminders, giving you all the support and guidance you need. These range from annual ‘health check’ site visits by your dedicated Technical Manager to providing general maintenance schedules and tailored cleaning plans for your roof. Our approved contractors can also offer yearly maintenance contracts.
Garland UK Technical Managers have a wealth of experience and are always on hand to help you choose the right metal facade system for any project’s requirements.
Metal facade systems provide impressive aesthetics, design flexibility, ease of installation, and exceptional performance and are the most sustainable building envelope solutions available. They are cost-effective, and with their long lifespans and effective end-of-life recycling, they form a truly circular economy, leading the way in sustainable building practices.
Daniel Simpson, Technical Manager, Garland UK