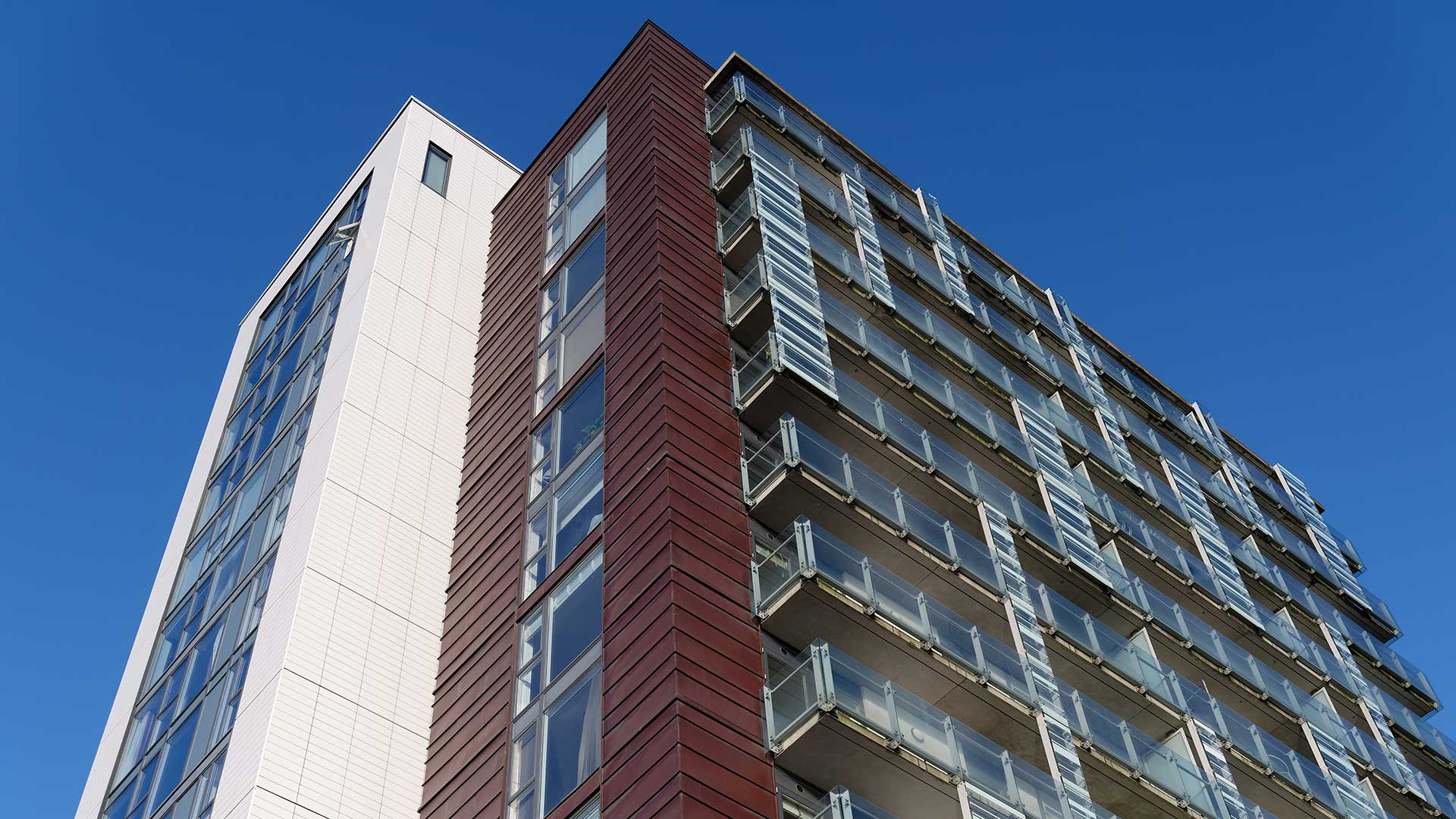
Since the tragic event of the Grenfell Tower fire in London on June 14, 2017, the issue of unsafe cladding and facades has catapulted into the public eye and exposed serious deficiencies in the safety of building materials used in construction.
Many factors contributed to the tragedy of Grenfell, three of which need to be considered for every retrofitting cladding or facade project. These were the cladding material, fire spread, and inadequate fire safety measures.
Grenfell Tower was clad with an aluminium composite material (ACM) panel with a highly flammable polyethylene core. Alongside this, the cavity barriers intended to prevent fire spread in the ventilation gap were insufficient and, in some cases, incorrectly installed. The final issue was that there were inadequate methods to tackle the fire within the building, including a lack of sprinklers and only one escape route.
In this article, the emphasis will be on the first two aspects of fire safety in facades and will delve into the considerations that must be taken when dealing with cladding refurbishment projects.
Before determining a replacement option, it is crucial to discover whether the cladding replacement is necessary. A comprehensive approach is essential to assess if a building’s cladding is unsafe and requires replacement, encompassing visual inspections, documentation review and potentially specialised testing. The initial step involves reviewing As-Built drawings to identify the cladding build-up used in the construction. Subsequently, a comparison is made between the identified cladding and current building regulations to ensure compliance.
If it is not possible to obtain the As-Built drawings or they are unclear, then a cladding expert can visually identify the cladding. They will be able to help identify the type of cladding being used and can look for signs of wear, damage and deterioration. If the cladding expert flags a potential issue, then a qualified fire safety surveyor should be appointed if potential combustible materials are identified. They will then conduct a full survey and produce an EWS1 form with an outcome of either Option A or Option B.
Option A is for buildings with an external wall system that is unlikely to support combustion. Option B signifies that combustible materials are in the facade, and the fire engineer must proceed to conduct a risk assessment. From here, the assessment will categorise the fire risk as either negligible or necessitating remedial works. If remedial works are advised, then a compliant specification needs to be written for the replacement of the cladding.
The first step in creating this specification is to undertake a structural analysis of the existing building. There should be two areas of focus within the analysis. The load-bearing capacity of the existing structure to understand if it can support the proposed cladding system. This is followed by an assessment of the building’s foundation to ensure it can handle additional loads to the building. This is specifically important when changing from a lightweight metal cladding to a masonry/stone facade system.
The type of materials used for the sub-structure of the existing facade will be conditional on the age and location of the building. This is important as materials that are being proposed need to be compatible with the existing structure so that they will not cause issues like corrosion or degradation. Another essential aspect of compatibility with the existing structure is the materials’ thermal expansion and contraction. It needs to be ensured that there are no imbalances or that precautions are taken to allow this expansion to manifest without risk to the facade.
A common issue with retrofitting facades onto masonry is that there is unlikely to be a sufficient fixing point to suit the new system’s structural and wind loading requirements. In this case, a ‘Slab to Slab’ system can be used, a bulked-up version of a helping hand and rail system. With this method, the helping hand brackets are fixed into the structural floor slabs, and the rails span between the two, removing the need for a fixing point in the masonry or other lightweight secondary structure. This has other benefits, such as removing labour costs and the number of brackets required.
A bespoke sub-frame specification should also be established to fix the new facade system at this stage. Whether it is integrating an existing Steel Framing System (SFS) or utilising a ‘Slab to Slab’ system, the subsequent consideration is determining the size of the void to house the new insulation. For this, an architect or surveyor might have a specific thermal U-value in mind. Alternatively, without a specified U-value, Building Regulations Part L should be used to get the appropriate thermal efficiency for the facade.
When aiming for a specific U-value target, it’s essential to consider the selection of insulation type and thickness and evaluate the effects of the sub-frame on thermal bridging throughout the facade. The thermal conductivity (Lambda-Value), vapour permeability, hydrophobic properties, density and compression, durability, acoustics and most importantly, fire safety must be considered when picking an insulation for a retrofit project.
After selecting the appropriate insulation with a specific lambda value (ƛ), most facade sub-frame providers can suggest a suitable bracket height and layout to accommodate wind loadings, meet the required U value, and allow for the necessary ventilation gap. In comparison, one bracket may seem more expensive than another as an individual item. However, some brackets exhibit superior resistance to thermal bridging, allowing the decrease of insulation depth to achieve the same U-value. Therefore, evaluating the market comprehensively and considering the entire facade cost is crucial rather than relying solely on an individual bracket cost comparison.
The ventilation gap in contemporary facade systems plays a crucial role in the building’s moisture management and temperature regulation. Its design should adhere to the manufacturer’s guidance, contingent on whether the panel joint is open or closed. While the ventilation gap offers significant advantages, it also poses a vulnerability regarding fire safety. As highlighted earlier, incorrect compartmentation within the ventilation gap can serve as a direct pathway for fire to spread throughout the building.
It is the responsibility and role of a certified fire engineer to develop a fire compartmentation strategy, incorporating vertical and horizontal fire barriers in the facade to halt the spread of fire. If this strategy is formulated after the initial design layout of the helping hand brackets, it must be reassessed to guarantee alignment with the compartmentation plan. This becomes especially critical around windows and penetrations.
At this juncture, the material type and design for the new facade should also align with planning parameters. The facade system’s recyclability, design for disassembly, and durability should be considered to ensure longevity and help aim for the most sustainable option available.
Depending on the height of the building and other factors outlined in Approved Document B will determine whether the finalised build-up will need to be submitted for a BS 8414 test. The British Standard provides a test method for assessing the fire performance of an external cladding system applied to the face of a building and subjected to a simulated fire. Specifically, it focuses on the fire performance of the cladding system as a whole.
BS 8414 is a full-scale test which is typically conducted in a specialised testing facility. It simulates a fire on the external face of a building, assessing the performance of the cladding under specific conditions. It especially focuses on how the fire may propagate vertically through the facade system, especially in the presence of combustible materials such as cladding and insulation. By replicating a real-world scenario, the test provides a more accurate representation of how a fire might behave on the facade. Even if it is not a requirement for a project, the test result will demonstrate valuable guidance to designers, architects and building surveyors when selecting cladding systems.
However, a notable challenge with this test is the potential for misrepresentation or misleading claims. This arises because the test solely represents the exact build-up that underwent testing, rendering any insulation thickness or bracket-type alterations outside the test’s coverage. Nonetheless, BS 9414 outlines procedures and regulations for assessing variations and modifications to products and systems previously tested in accordance with BS 8414‑1:2015+A1:2017 or BS 8414‑2:2015+A1:2017. It also defines options and limits for generating reports based on the provided direct and extended application criteria.
Retrofitting unsafe cladding and facades requires a meticulous and comprehensive approach, where the critical factors of cladding material, fire spread, and inadequate safety measures must be thoroughly addressed in any refurbishment project.
When embarking on a cladding replacement project, a collaborative approach should be taken, including the instruction of structural and fire engineers to ensure the system design and installation are safe and compliant at every stage. Working with Garland UK and utilising the A1 fire-rated R-MER Shield metal rainscreen system ensures that facade replacements meet the highest safety, regulatory compliance and durability standards.
Garland UK Technical Managers are your first port of call if you are considering retrofitting unsafe cladding or facades at your building. Sharing extensive technical expertise and guidance on managing your project with high-performance rainscreen systems that are installed safely and to the highest professional standard, all supported by our leading 30 year Single-Point Guarantee.
Jack Costello, Technical Manager, Garland UK