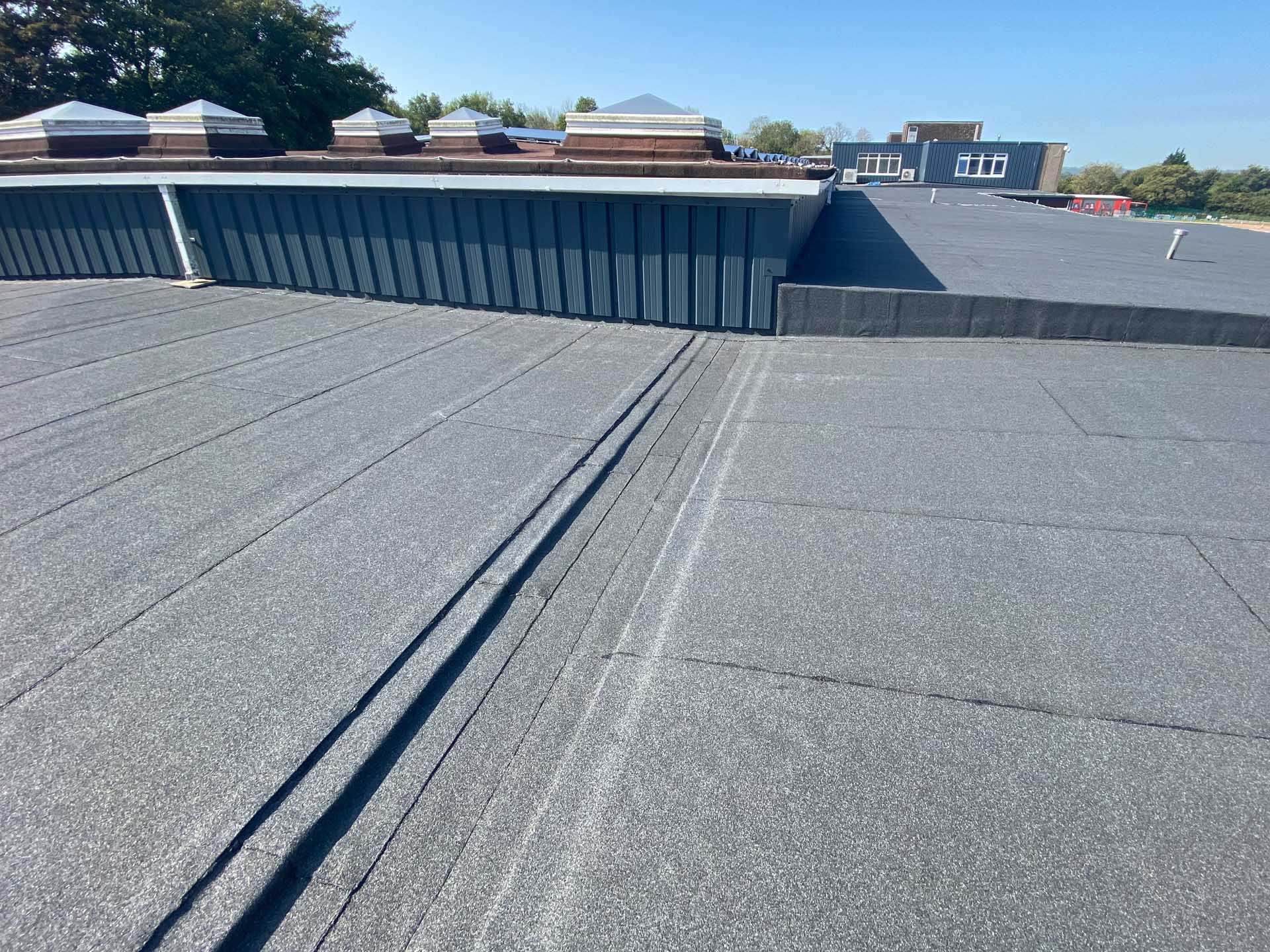
There are a variety of different membrane roofing solutions available on the market today. These can generally be separated into two distinct groups, single-ply synthetic membranes and modified bitumen multi-layer systems.
We discuss the main differences between these two groups, from the number and type of waterproofing layers utilised in the roofing system, whilst providing distinct advantages and disadvantages for each.
To help you make the best decision for your roofing asset, we have compiled the key features of both synthetic single-ply and bitumen membranes to consider.
Single-ply membranes are factory manufactured synthetic sheet materials most commonly made from, ethylene propylene diene monomer (EPDM), polyvinyl chloride (PVC), thermoplastic polyolefin (TPO) and thermoplastic polyolefin elastomer (TPE).
These materials fall into two categories, thermosetting polymer (known as thermoset) and thermosoftening plastic (known as thermoplastic). Of the four, EPDM is the only thermoset material whilst PVC, TPO and TPE are all thermoplastics. Thermoset does not soften when heated in contrast to thermoplastic which will soften and can be reshaped when heat is applied. This and other chemical properties mean differing techniques are used in installation and each material has distinctive performance characteristics.
All membranes can be chemically adhered, mechanically fixed or ballasted to your roofing structure to provide a single layer of waterproof protection.
Modified bitumen membranes combine bitumen and styrene-butadiene-styrene (SBS), a family of synthetic rubber originating from styrene and butadiene. This process modifies the bitumen to create a copolymer with vastly improved elasticity, tensile strength, abrasion resistance, ageing stability and a higher softening point whilst retaining the phenomenal waterproofing performance of bitumen. The SBS modified bitumen is integrated with reinforcing mats consisting of polyester, fibreglass, or a composite of the two, to form the finished membrane
Modified bituminous systems utilise two layers of factory manufactured SBS modified bitumen sheet material. Firstly, an underlayment is applied to your roofing structure, followed by a cap sheet with a mineral slate finish for added UV protection and an improved aesthetic finish.
These are available for either torch-on or self-adhesive roofing applications. The resulting system provides multiple layers of high-performance waterproofing protection.
By only using a single layer of waterproofing all single-ply systems use fewer materials, making them comparatively cheap. The single-layer also allows for a faster installation time. Installation is relatively easy, requiring less training for contractors and fewer specialist tools. The single layer of thin material also minimises the thickness of the roof construction and the materials themselves are lightweight.
In addition to these shared traits, each membrane has its own individual advantages.
EPDM comes in very large sheets meaning there are fewer seams.
PVC is available in a lot of colours, is extremely flexible and has additives to increase its fire resistance and UV protection. A seam can be easily heat welded.
TPO is an excellent heat reflector, especially when the white coloured option is used.
It incorporates a laminated top layer of UV protection and fire-resistant additives. It can be heat-welded at the seams by skilled installers.
TPE is basically an improved version of TPO. It is UV stable and fire-resistant throughout. It is more forgiving of dust and dirt when heat sealing, improving seam strength.
Using such thin materials has a significant drawback, all single-ply roof membranes are extremely easy to puncture. This means that they cannot withstand foot traffic and seriously inhibits maintenance access. Having only one level of adhesion, being directly installed onto the roofing substrate, and combined with their light weight makes them very susceptible to wind uplift, particularly on poorly sealed seams. If the system is chemically adhered to the roofing substrate then, due again to the thin construction, the adhesives used can degenerate quickly due to UV and thermal heating. As a result of these issues, the lifespan of single-ply roofs can be surprisingly short.
Perhaps the most obvious and significant disadvantage that they all share is the very fact that they are single-ply membranes. There is no built-in redundancy within these systems; any puncture, faulty seam or other failures in the membrane will immediately lead to water ingress into the roofing substructure and the building itself.
Another disadvantage is that a single layer of membrane does not allow the roofing details to be independently waterproofed, allowing the roof to be compartmentalised section by section which reduces the risk of whole roof failure in the long run.
In addition to these shared traits, each membrane has its own individual disadvantages.
EPDM has no UV protection, leaving it extremely vulnerable to early degradation, shrinking and stretching. Seams are joined with a primer and adhesive which has a tendency to fail quickly. Seam failure is so common that some systems incorporate an additional cover tape adhered over the seam, but this too is prone to failure when it laps a perpendicular seam or over laps more cover tape. This susceptibility to seam faults means that it copes poorly with complex roof details. EPDM is not fire-resistant and has very poor resistance to oils, fats and grease.
PVC contains plasticiser. This will leech over time leading to shrinkage which can cause seams to fail and cause lifting from the roof substructure. It also causes the PVC to become very brittle over time and in cold weather, it is known to shatter causing the roof to fail.
TPO cannot be heat welded successfully when dusty or dirty, which can be very hard to maintain during installation, leading to an increased likelihood of seam failures. It is susceptible to damage from thermal heating, resulting in shrinking which again leads to failures at the seams and lifting from the roof substructure. The laminated top layer that provides its UV protection and fire resistance can also introduce weaknesses making the TPO more prone to crazing and subsequent deterioration. Exposure to any petroleum-based product will cause TPO serious damage.
TPE whilst an improvement on TPO is still susceptible to thermal heating, which can lead to shrinkage and seam failure. Again, it is particularly vulnerable to exposure to any petroleum-based product which will cause TPE serious damage.
As we touched on earlier, the SBS copolymer used to make modified bitumen membranes has some pretty phenomenal characteristics. Resulting in a solution that can have far greater tensile strength than any single-ply membrane, whilst remaining extremely flexible, both for ease of installation and to reduce its exposure to thermal heating as well as movement within the roofing structure. The high performance modified bitumen membrane is extremely durable allowing it to withstand greater levels of fatigue over long periods of time. This durability allows for foot traffic, making maintenance access considerably easier.
Bituminous membranes are available for torch-on application and for self-adhesive application and of course, a combination of both is possible for different layers. Both techniques in effect allow for the various layers to fuse together into one homogenous bitumen mass, making seam failures and wind uplift less likely. The ability of the bituminous membranes to be easily worked with heat makes repairs quick and easy.
With mineral slate incorporated as the external finish on the cap sheet, Garland UK’s modified bituminous membranes have excellent UV resistance and have achieved a fire classification of Broof(t4) to EN13501-5 when tested as one of our built-up modified bitumen systems.
The most significant advantage that modified bitumen systems have, is the amount of redundancy that is built-in to the system. By utilising multiple layers of membrane, not only do you increase the strength of the whole system, making it incredibly resistant to both punctures and building movement, but you also provide two layers of waterproofing. This means that a failure in one layer, will not lead to water ingress into the roof substructure or the building itself.
The multiple layers also allow for detailing to be made independently, creating safety breaks within the waterproofing system which prevents water tracking from detail to detail should the roof be compromised.
All of these advantages combined mean that modified bitumen systems have an exceptionally long lifespan, far in excess of any single-ply membrane in a real-world environment.
There is no getting around the fact that multi-layer bituminous systems do have some disadvantages. Due to the fact that there are multiple layers of the membrane to install there are increased materials costs and installation will take longer than for single-ply membranes. However, this does mean that with more layers applied in the system, greater waterproofing protection is added to the roof.
Highly trained installers must be used to ensure that the modified bitumen membranes are correctly installed and that complex roof details are carried out to the highest standards. Whilst safety on site is always paramount, torch-on applications need extra care, ensuring that the NFRC Safe2Torch checks are performed and guidance is followed at all times to reduce the risk of a roof fire.
Garland UK can help with this last issue. We have a national network of highly skilled Approved Contractors, with extensive expertise and training, you can trust to complete your work safely and to the highest professional standard, all supported by our up to 30 years Garland UK Single-Point Guarantee.
Garland UK only supplies multi-ply solutions to your roofing needs. It is our belief that single-ply options have become something of an anachronism in the industry. With no built-in redundancy in their design, susceptibility to punctures and other failures, single-ply membranes cannot compete with multi-ply bituminous membranes with exceptional durability and lifespan. Modified bitumen membranes can be trusted to last the test of time.
Garland UK is committed to only providing roofing solutions in which we have complete confidence, with a mission to raise standards in the industry and do the right thing for our clients. For your complete peace of mind, we support all our modified bitumen systems covering up to 30 years with our industry-leading Single-Point Guarantee.
Garland UK produces a wide variety of modified bitumen membranes, allowing for bespoke solutions to your particular roofing needs. Our dedicated Technical Managers are your single point of contact and are always on hand to help you find the right combination for you.
“Whilst single-ply options may seem on the surface like a cost-effective choice, we know that multi-ply systems have the built-in redundancy to keep your roof leak-free and your building protected for the long-term.”
Daniel Simpson, Technical Manager, Garland UK